Construction of your dream home starts with selecting and procuring materials that form the building blocks of the process. Procurement is basically a part of material management that involves planning, executing, and controlling related activities on the site. Materials used in construction can be in various forms like solid, semi-solid, liquid, processed, or unprocessed. Their availability, suitability, costing, and environmental impacts should always be considered before selection.
Building a house is not just the erection of four walls and a roof, but a complete process starting from planning and ending with appropriate execution. The basic structure of the house is built in accordance with the architectural design requirement, and each facet of this structure is forged using a variety of raw as well as man-made building materials.
The material engineers on-site possess an in-depth knowledge of all these products and consider a variety of factors in their procurement like cost, product performance, aesthetics, carbon footprints, energy efficiency, and more. The three main aspects that govern procurement are selection, specification, and quality control of materials.
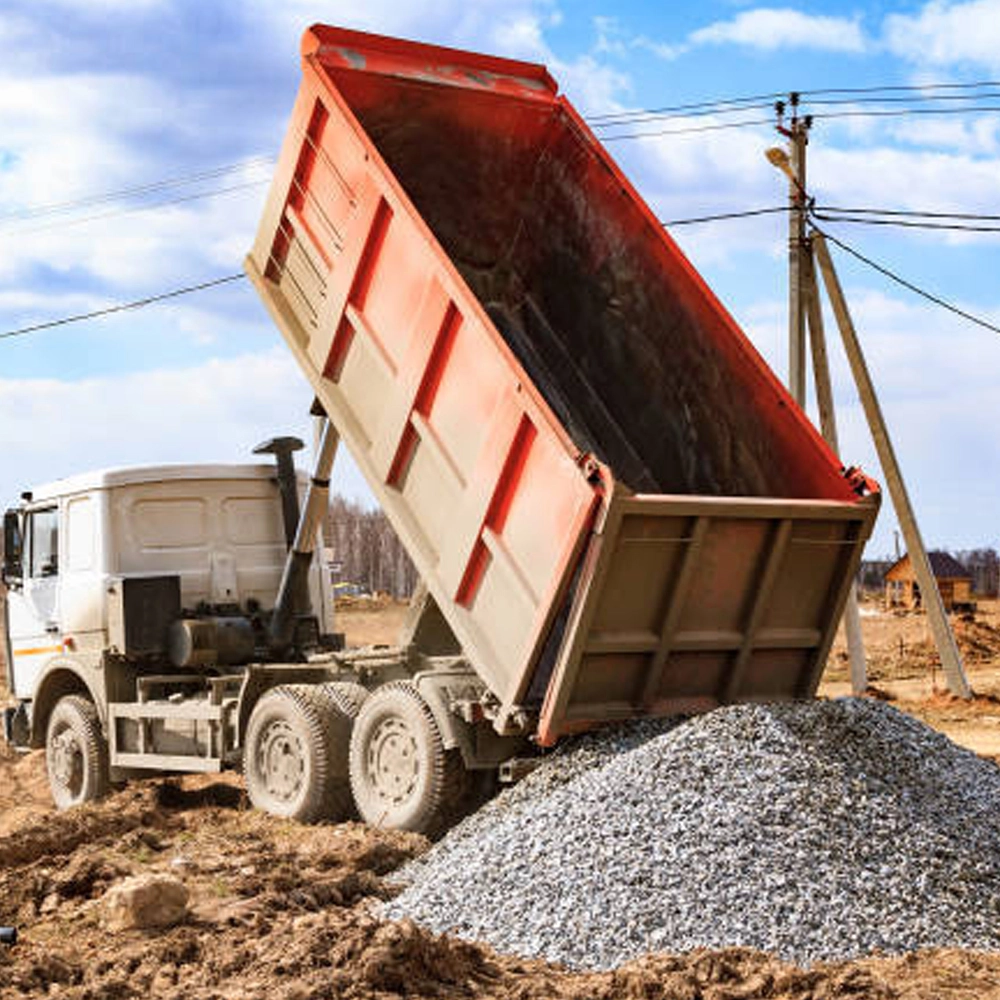
An interruption in the acquisition process may lead to a delay in work, a compromise in quality, or fluctuation in the material costing. Therefore understanding the various factors and the process involved in material procurement is necessary, so that you can prioritize your requirements and they can easily be communicated to your builder.
Let us go through each of these factors in detail:
1. Material Planning
This includes identification of the types of materials to be used, their costs, and communication of the budget according to the quality required by the constructor. By employing durable and high-quality materials in your house, you will clearly see an impact on its functionality and outlook in the long run, as well as have a surety on the longevity of the building structure.
The primary and fundamental components required for construction are aggregates (coarse and fine), bricks, wood, cement, masonry, etc. A good mixture of coarse and fine aggregates gives more strength and resistance to concrete.
2. Vendor Analysis
The choice of vendor is directly related to the cost of material, the quality required, and time associated with the whole supply process. Rates are decided according to the varying quantities and groups of materials. A contractor may judge the vendors with respect to the competitiveness of the price offered and timeliness of delivery.
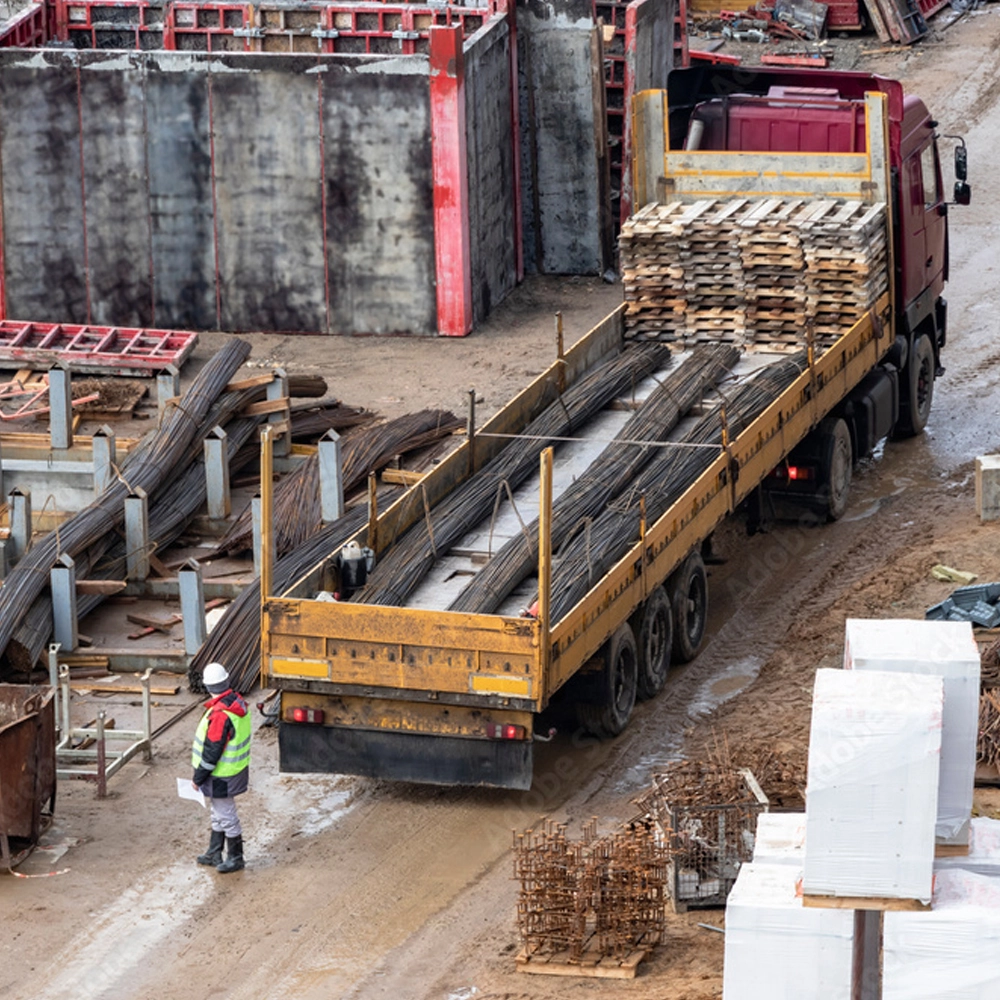
The chosen vendor should be agreeable to any defects, returns, or reworks along with being trustworthy. Cost and quality should be predetermined, to maintain good relations with the vendor in the future.
3. Quality of the Materials
A project’s durability and the quality of materials used are highly co-related. High-quality materials are quite sustainable and add more life to the project, making it strong and efficient to face environmental catastrophes. These superior-quality materials involve low maintenance as they rarely get damaged from any wear and tear, and they also help eliminate any need for replacement.
They may seem to rip off the budget initially, but they save a lot of repair and maintenance costs in the long run, and increase the home value instantly at the time of resale if the need arises.
4. Storage and Inventory
The material ordered should be stored in a safe place where it can be protected from any damage or unwanted hazards. An area on the construction site itself should be made vacant for the storage of inventory so that the workers have access to materials at any hour. The quantity of stock is planned by the materials manager by analyzing the requirement of the project. An accurate analysis will lead to the optimum purchase of the materials and eliminate any wastage or delay in delivery.
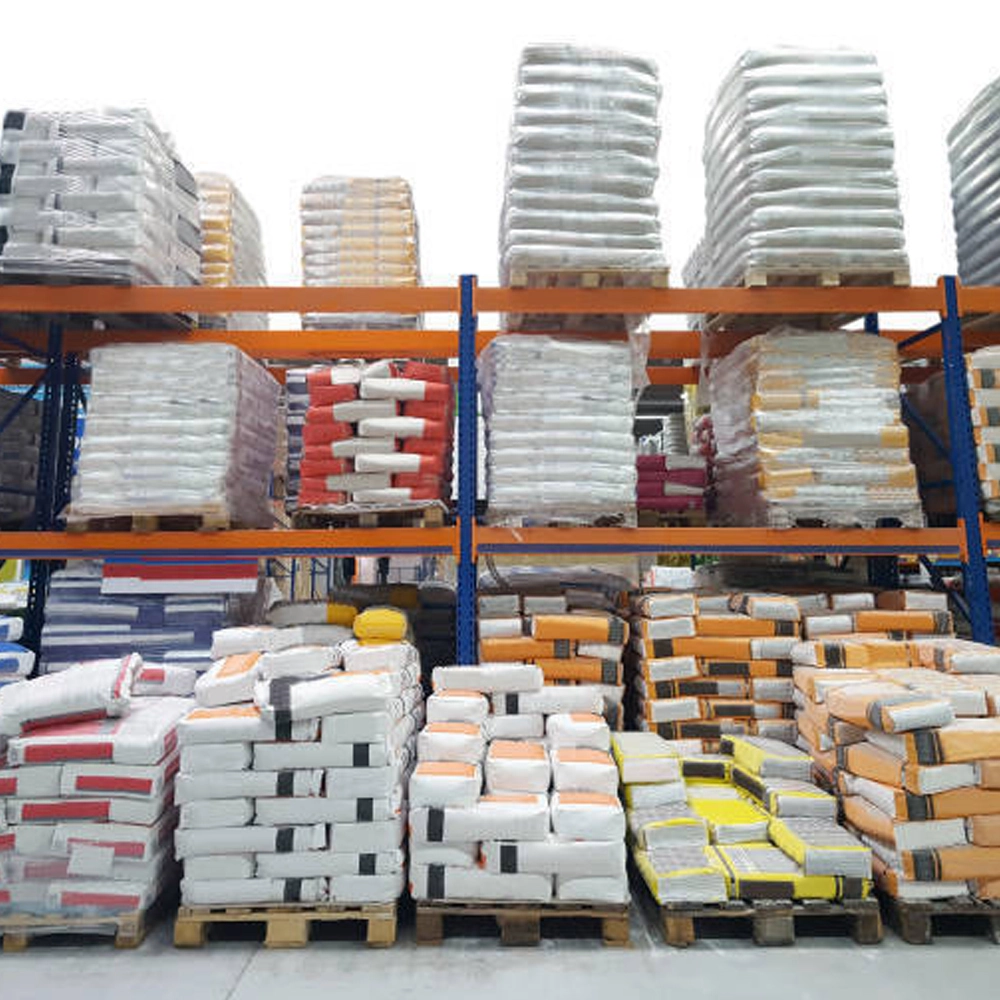
5. Material Purchasing
Significant problems in material purchasing are unavailability and inconsistency in the delivery timeline. The materials purchased may not match the specifications and the quantity ordered which is due to a lack of communication between suppliers and contractors. Therefore, contractors should always be mindful of these issues and keep checking the integrity of each step of material procurement, as any differences may hinder the whole process of construction.
6. Supply, distribution, and on-site
Distribution of materials to various activities and on-site usage sometimes leads to damage or mishandling of products. This scenario arises when the labor employed is either not trained or unskilled and may use excessive material or incorrect products which may not belong to that respective activity. It is essential to ensure that each and every product gets distributed in the right quantity and assigned to the activity for which it is purchased, along with training the labor to use it effectively on-site.
The ultimate goal behind getting a deep understanding of each and every aspect of material procurement is to obtain the right material in the exact quantity needed and in the right time duration, without any wastage or mishandling of the products. Your budget and varied needs for your house construction should be communicated to the contractor well before starting the work so that he can take informed and suitable decisions.
Make My House helps you to understand all the prerequisites related to procurement and stands with you at every step of the process.
One thought on “Factors Affecting Material Procurement in House Construction”